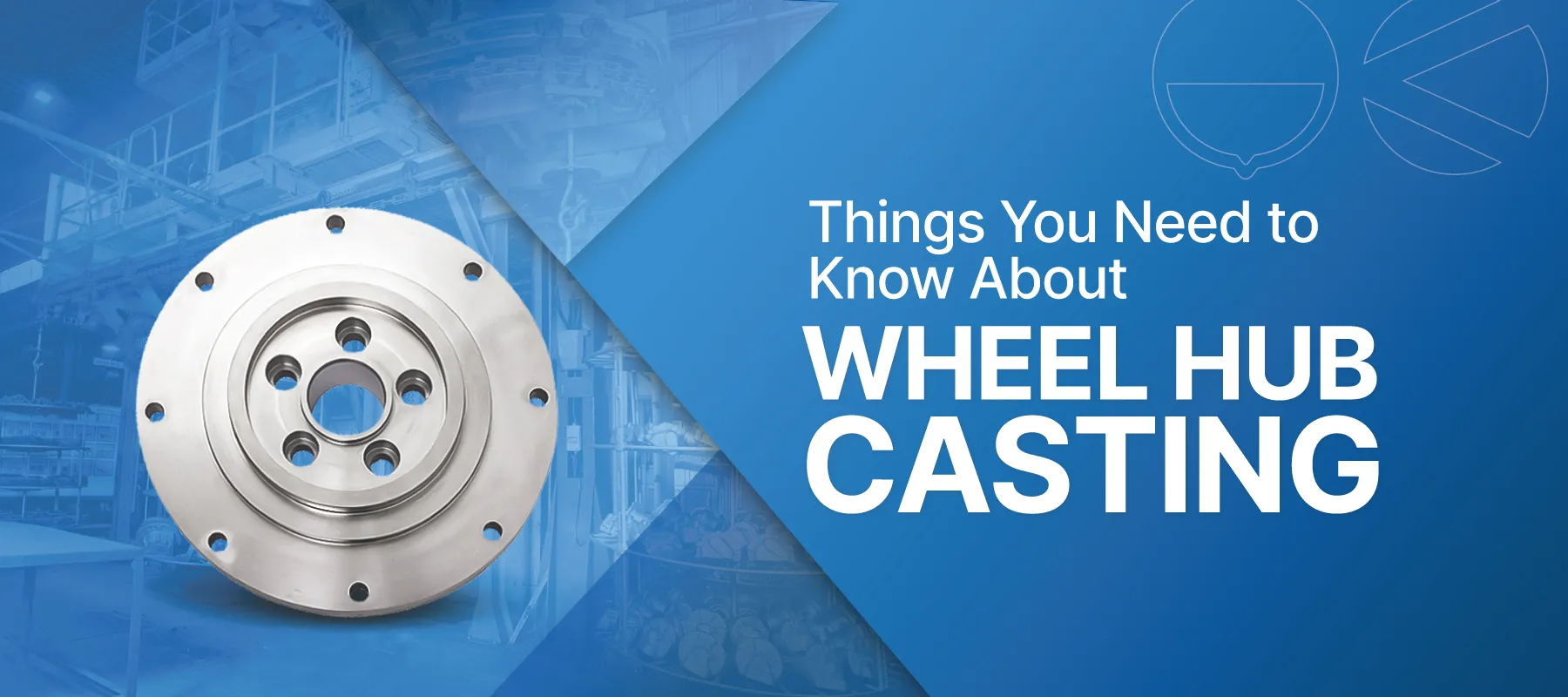
Things You Need to Know About Wheel Hub Casting
Wheel hub casting is a critical process in the manufacturing of vehicles, playing a key role in ensuring the safety, Performance, and Durability of Automobiles. The wheel hub is the central part of a car's wheel that connects the wheel to the axle, allowing for smooth rotation and supporting the weight of the vehicle. Understanding the intricacies of wheel hub casting is essential for anyone interested in automotive engineering, manufacturing, or maintenance. In this blog, we will explore the fundamental aspects of wheel hub casting, including the materials used, the casting process, and the importance of quality control.
Materials Used in Wheel Hub Casting
The choice of materials is crucial in wheel hub casting as it directly affects the performance and longevity of the wheel hub. Common materials used include:
Grey Iron : Known for its excellent castability, damping capacity, and machinability. It is often used in applications where noise reduction is essential. Grey iron's graphite microstructure gives it good vibration damping and wear resistance properties.
Ductile Iron : Offers superior strength and toughness compared to grey iron. It is used in high-stress applications due to its ability to withstand significant mechanical stress. The nodular graphite inclusions in ductile iron give it a combination of strength, plasticity, and wear resistance.
Aluminium Alloys : Lightweight and corrosion-resistant, making them ideal for performance-oriented and high-efficiency vehicles. They provide a good balance between strength and weight. Aluminium wheel hubs can enhance fuel efficiency due to their lighter weight.
Steel : Provides high strength and durability, though it is heavier than aluminium. It is often used in heavy-duty and commercial vehicles where strength and load-bearing capacity are critical. Steel's robustness makes it suitable for environments where the wheel hub is subjected to heavy loads and harsh conditions.
The Wheel Hub Casting Process
The casting process involves several key steps, each of which must be meticulously controlled to ensure the quality of the final product:
Pattern Making : A pattern created based on the design of the wheel hub. This pattern used to create the mould in which the casting will be poured. The pattern can be made from wood, plastic, or metal, and must accurately represent the final wheel hub, including any allowances for shrinkage during cooling.
Mould Making : The mould is made from sand, ceramic, or metal, depending on the specific requirements of the casting process. The mould must be precise to ensure the accuracy of the wheel hub dimensions. Sand moulds are typically used for single-use applications, while ceramic or metal moulds may be used for higher precision and repeated castings.
Core Making : Cores are used to create any internal cavities or complex shapes within the wheel hub. These are typically made from sand and must be placed accurately within the mould to ensure the final casting meets design specifications.
Melting and Pouring : The chosen material is melted in a furnace and poured into the mould. This step requires careful control of temperature and pouring speed to avoid defects such as gas porosity or incomplete filling of the mould. The molten metal must be at the correct temperature to ensure fluidity and minimize the risk of defects.
Cooling and Solidification : The molten material cools and solidifies within the mould, forming the wheel hub. The cooling rate must be controlled to prevent internal stresses and defects. Controlled cooling is essential to achieve the desired microstructure and mechanical properties in the final casting.
Removing the Casting : Once solidified, the casting is removed from the mould. This may involve breaking the mould if it is a single-use sand mould. For reusable moulds, careful handling is required to ensure the mould can be used for subsequent castings.
Finishing : The casting undergoes various finishing processes such as cleaning, grinding, and machining to achieve the desired surface finish and dimensional accuracy. Any excess material, such as gates or risers, is removed, and the casting is machined to meet precise specifications.
Heat Treatment : Depending on the material and required properties, the wheel hub may undergo heat treatment processes such as annealing, quenching, or tempering. These processes improve mechanical properties like hardness, toughness, and ductility.
Quality Control : The final step involves rigorous inspection and testing to ensure the wheel hub meets all specified requirements. This may include dimensional checks, material testing, and non-destructive testing techniques like X-ray or ultrasonic inspection. Ensuring the quality of the casting is critical to the safety and performance of the final product.
Importance of Quality Control
Quality control is paramount in wheel hub casting to ensure the safety and reliability of the vehicle. Defects in the casting process can lead to issues such as cracks, porosity, and dimensional inaccuracies, which can compromise the integrity of the wheel hub. Implementing stringent quality control measures helps in identifying and addressing potential issues early in the process, thereby ensuring the production of high-quality wheel hubs that meet industry standards.
Non-destructive testing methods, such as radiographic (X-ray) inspection and ultrasonic testing, allow for the detection of internal defects without damaging the component. These methods are essential for ensuring the integrity of the wheel hub and preventing failures in service. Additionally, mechanical testing such as tensile, hardness, and impact tests provide data on the material properties and ensure they meet the required specifications.
Advances in Wheel Hub Casting
Technological advancements have significantly improved the wheel hub casting process. Innovations such as computer-aided design (CAD) and computer-aided manufacturing (CAM) have enhanced the precision and efficiency of pattern and mold making. These tools allow for the simulation of the casting process, predicting potential issues and optimizing the design before production.
Additive manufacturing (3D printing) has also made inroads in casting, particularly in the creation of complex patterns and cores. This technology allows for the rapid prototyping of designs and can significantly reduce lead times.
Modern inspection techniques like 3D scanning and real-time monitoring have further ensured the consistency and quality of cast wheel hubs. 3D scanning can compare the physical casting to the digital model, ensuring dimensional accuracy and identifying any deviations early in the process.
Environmental Considerations
Sustainability is becoming increasingly important in manufacturing processes, including wheel hub casting. Foundries are implementing more environmentally friendly practices, such as recycling scrap metal, reducing energy consumption, and minimizing waste. Advances in material science are also leading to the development of more sustainable alloys that offer high performance with lower environmental impact.
Using advanced simulation software, manufacturers can optimize the casting process to reduce material waste and energy use. For example, by simulating the flow of molten metal within the mold, manufacturers can minimize defects and ensure efficient material use.
Conclusion
Wheel hub casting is a complex yet essential process in automotive manufacturing. By understanding the materials, casting process, and the importance of quality control, manufacturers can produce wheel hubs that ensure the safety, performance, and durability of vehicles. As technology continues to evolve, the casting process will become even more efficient and precise, contributing to the advancement of the automotive industry. Whether you are a professional in the field or simply an enthusiast, appreciating the intricacies of Wheel Hub Casting Can Deepen Your Understanding of vehicle manufacturing and the critical role this component plays in automotive safety and performance.
The ongoing focus on sustainability and innovation in wheel hub casting promises a future where vehicles are not only safer and more reliable but also more environmentally friendly. By staying informed about these advancements, stakeholders in the automotive industry can continue to push the boundaries of what is possible, creating better, more sustainable solutions for tomorrow’s transportation needs.