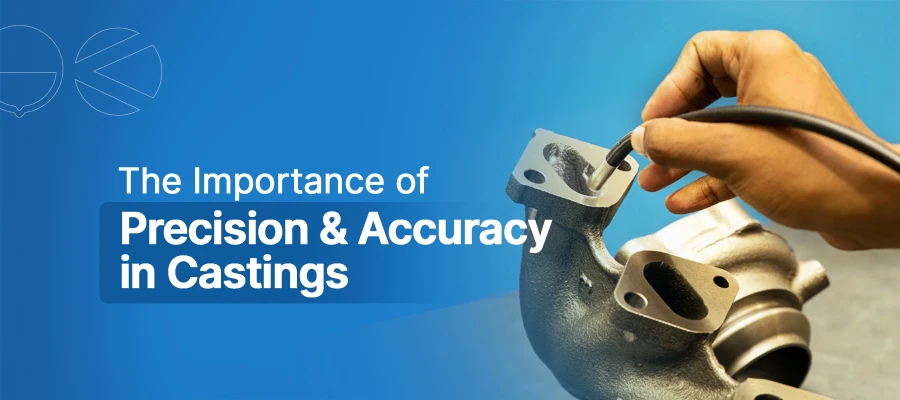
Casting Production: Everything You Need to Know
Casting is the fundamental process to every discovery of engineering products, including simple to intricate parts and components. From screws to the largest product comprising a mix of various products, without the processing of metal casting, there is no word for it.
Every industry significantly relies on the casting industry to meet different requirements to manufacture a product of any nature. Casting has never been the newest terminology added to the dictionary of the manufacturing industry.
As likely said, casting has established its importance since a few centuries ago. It has undergone numerous transitions and laid the foundation for the newest generation of manufacturing techniques and methods.
What is Casting?
As the terminology suggests, it coins the definition of melting a metal ore to derive the liquified form, pouring the obtained substrate into the predetermined mold and cooling it down to get the desired shape of a part and component.
The quality and efficiency of a casting product depend on the alloy combination and the technique implied at the foundry to cast. The alteration and addition of new forms of the alloy have uplifted the reliability of casting production to create a greater impact.
Though it is a conventional method, the sustainable solution with the latest upgrade has manifested its competitive advantage to symbolize even the current trends of the manufacturing industry.
Types of Casting
The industry has witnessed changes in the casting methodologies to produce new products. Limitations and problems underlie the primary cause factor fueling up the intent to derive a solution.
The restriction in casting production to meet technical requirements of defined parts and components has paved the way for the research and development of newer methods of casting production.
Here are some of the most commonly practiced methods of casting techniques.
Sand Casting
It is the most commonly used method of casting to produce products. The manufacturing method is still in practice.
The substances used in the sand casting process are chosen based on the molten alloy.
This production method has a competitive advantage of providing cost-effective solutions. Products with a design detailing of simple to moderate are manufactured with this casting method. Production flexibility is one of the key aspects of preferring this technique.
It has been the predominant choice for mass-volume production with less complexity. The process involves making a mold of the defined dimensions within the sandbox. Products and components that have a larger dimension are the best choice for sand casting.
But, it is quite a time consuming process which has been the major drawback of this method.
There is a requirement for additional tasks to fine-tune the produced product of the defined surface finish.
Investment Casting
This method has competitive advantages over other casting methods. Parts and components with intricate design detailing are manufactured with investment casting.
In the production process, products of minimalist dimensions with absolute precision and accuracy can not be achieved through die and sand casting. In such conditions, investment castings meet the technical requirements without exceeding the tolerances.
The complexity of a product with multiple manifolds and cross sections can be manufactured without defects.
Die Casting
Similar to sand casting, Die casting has been the best cost-optimizing manufacturing method. When it comes to large-volume production of the same part, the manufacturers rely on reusable molds.
Die Casting enables the advantage of casting production with the existing pattern and mold. The basic principle of this technique uses a low-wax coating applied on the interior surface of mold which melts when the molten alloy is poured into it for the production of castings.
However, the wax does not alter the physical properties of the casting product, which is the worth-noting characteristic of die casting. Henceforth, there is no chance for the tracing of produced molten alloy residue on the mold.
Die casting has the competitiveness of casting production of parts and components with the defined accuracy and precision and without exceeding the tolerances. In addition, compared to sand casting, Die casting provides better surface finish, restricting the additional requirement for finishing tasks.
The Choice of Casting Method
Based on the raw material, iron ore, alloy combination, and the complexity of product production, the casting method is determined.
In some cases, the chosen cast alloy will be suitable for manufacturing. Yet, the quality of the part and component influences the casting technique.
The comparison of results will add value to the investment made in the casting production.
The Bottom Line
We hope this article has provided you with useful information. JS Autocast is one of the reliable manufacturers of casting solutions; it has the production capabilities of die casting, sand casting and the latest casting techniques to produce products of the finest standards. Please visit https://www.jsautocast.com/index.php for more information.