Oil & Gas
Each and every equipment in the oil and gas Industry are designed and manufactured with a chosen quality as it is the major contributor to the world economy. Engineered, with high-quality equipment and tools witnessing the primary source of energy, our castings fit perfectly well with the most corrosive and demanding Oil & Gas environments. The offerings include impellers, diffusers, counterweights, and Mud Pump sets.
Impellers
Impellers
Cast Iron Impellers are one of the primary components of a pump, impacting its productivity and functioning. Bernoulli's principle is the fundamental working principle behind the operation of pumps, including centrifugal, vacuum, and many other variants of its kind. The increase in fluid velocity and decrease in pressure are the factors that are generated in the pumping operation.
When a transferring substance (gas or fluid) is passed through the impeller pump, the medium between the impeller vane and the pump wall escalates the working condition, resulting in increased velocity. This happens when the fluid or gas is in transit from the center to the outlet of the Impeller Casting. The transport medium loses its velocity and gains pressure when it attains the specified point prior to the outlet. The discharge of fluid takes place at an increased pressure from the impeller and pump orifice. The output efficiency of the pump is impacted by the Cast Iron Impeller's rotational speed and vane height.
Characteristics
Cast iron impellers are designed and engineered to satisfy the pumping requirements when the medium is transferred using pumps. Impeller Castings are preferred in the manufacturing of axial, radial, and mixed-flow pumps. The structural detailing and design of the pump impeller casting primarily depend on the flow that a pump discharges or deploys.
- Axial Flow Impeller : The medium is pumped parallel to the impeller.
- Radial Flow Impeller : The transferring medium is pumped at a 90-degree angle to the placement of the impeller.
- Mixed-Flow Impeller : It has the combined functionality of axial and radial flow. The angle of flow to the Impeller Casting is not similar to the radial flow.
We, the Manufacturer of Cast Iron Pump Impeller, have the facilities to cast the product of the various types with the defined specifications.
Diffusers
Diffusers
Cast Iron Diffusers are the components that hold a special function in minimizing the fluid pressure when the medium is transported through pumping. The working principle follows the reduction of fluid kinetic energy that is typically generated due to the changes in flow angle in the pipeline. The installation of Cast Iron Diffusers does not result in the generation of additional energy. The functioning of the diffuser castings is unaffected, irrespective of the fluid or medium type that is transferred. The component is primarily designed and engineered in such a way that it enables adiabatic
Iron-Cast Diffusers are most commonly installed in air handling systems to deduce the velocity and speed of airflow. Whereas, the impeller delivers the inverse function of the diffuser.
Diffuser Castings are a critical component that has a pivotal role in impacting the efficiency and productivity of the pumping system. In a typical design, the diffusers are attached next to the output phase of the impeller to reduce the flow velocity. There are applications where Cast Iron Impellers and Diffusers are installed within the assembly line. These components are preferred in creating a suitable working condition to transfer the medium. We, the Manufacturer of Diffuser Castings, ensure the produced cast products comprises the required specifications.
Transmission Parts
Transmission Parts
Flange Hubs
A Flange Hub Iron Casting is a component, preferably made of iron castings. It plays a pivotal role in connecting the other parts, such as a wheel, pulley, or sprocket. The structure of a Flange Casting has a flat steel plate provided with mounting studs to ensure a jointing point to connect the other parts parallelly, enabling the flange to function smoothly during rotation. The casting part allows the operator to refurbish the damaged bearing with ease.
The Flange Hub Iron Casting is manufactured and machined precisely with a smooth and flat surface to allow a straight-running attachment. The dimensional tolerances of the engineered flange hub are inspected to restrict any chance of creating wobbles or runs off-center. The overall efficiency and life expectancy are enhanced when the flange hub is cast precisely with defined detailing. The Ductile Iron Hub Casting part attached to the wobbly assembly of the belt or chain resists premature wear when the part is rubbed against the assembly side. We, the Flange Casting Manufacturer, practises globally renowned casting techniques to produce the best quality Cast Iron products.
Working Principle
The hard pressing of the opposite surfaces at the calculated pressure or strain produces a flange. The leak-tight seal is manufactured by applying force to the two faces of a flange. The defects on the faces lead to a significant drop in performance. A softer material, such as a gasket, is preferred in flange sealing for firm connection and to eliminate the occurrence of errors in sealing.
Other Applications
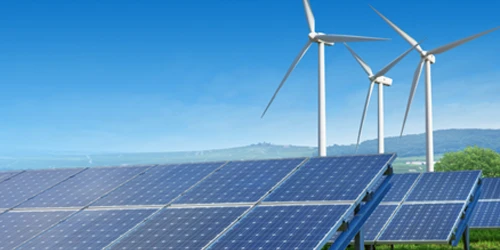
Wind Energy
The Worldwide wind market is becoming a vital source of power generation with a lesser carbon footprint.
View More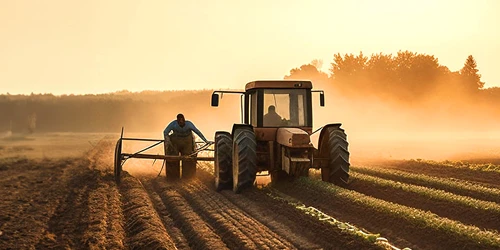
Agriculture
Manufacturing castings for the agricultural segment needs specialized expertise to meet the desired requirements.
View More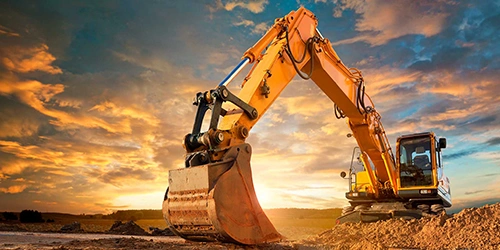
Off-Highway
The Off-Highway industry relies highly on large equipment and vehicles for operations and transportation.
View More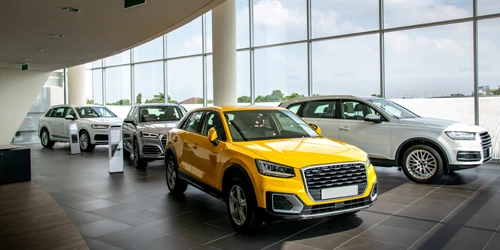
Automotive
The rapidly growing automotive industry in India is one of the largest in the world and it continues to grow at an incredible pace.
View More