
Equipped with HPML Disa Moulding Machines
With the availability of high-pressure DISA machines, jolt and squeeze as well as hand-molding equipment, we can humbly say that no complexity among DI castings is out of our coverage area.
Our molding process has kept at pace with the best practices and standards in the Foundry industry. Since we prefer moulds that have thermal conductivity and high heat resistance, the process defines the technical properties of output. The robotic grinding machines give us an edge over competitors w.r.t the casting finish.
Key Features
State-of-the-art DISA machines for moulding
- DISA Match – 20” X 24” with box size of 508X610X200+200
- DISA 2070-B with box size of 950X800X350~650
- DISA flex 90 with box size of 1200X900X400+400
- DISA George Fisher with Box size of 700X500X 200+200
- DISA MATIC 130B with Box size of 650x535x180~350
Sand Plant
- Intensive Mixer DISA TM285
- Sand Multi controller (SMC)
- Kunkel Wagner sand cooler – ASK 150
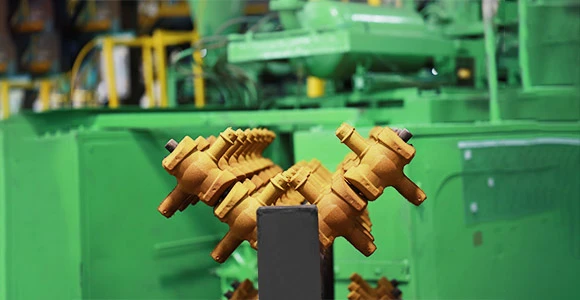
Core Shop
- Specialized in cold box, Hot box, Co2 core process.
- Core shooter capacities ranging up to 50kgs
- CO2 core weight up to 500kgs
- Cold box core shooter -Laempe
- Hot box shooters -SUSHA
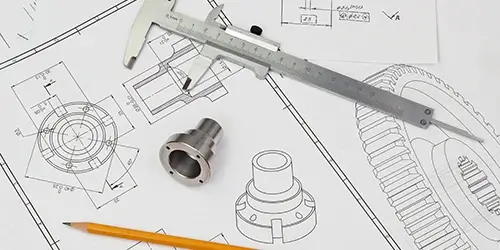
Design Engineering and Product Development
JS Autocast has an in-house team of professionals for casting design & simulation.
View More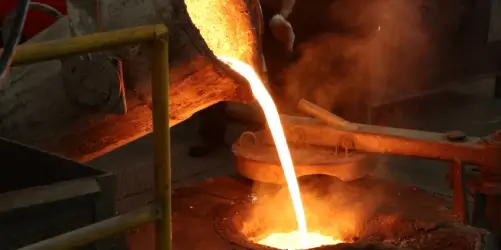
Melting & Pouring
We at JS Autocast are committed to adhere with the industry's best Metal Melting practices.
View More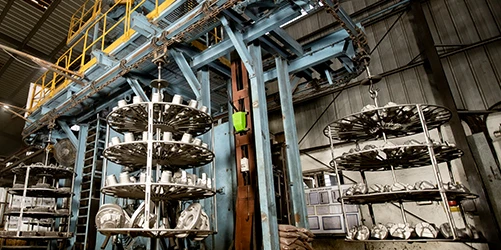
Post Production Process
We at JS Autocast are committed to adhere with the industry's best Metal Melting practices.
View More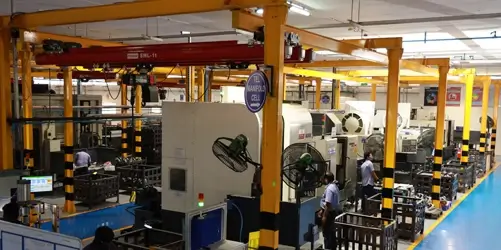
Machine Shop
The In-house machining capabilities gives us an unrivaled command over the quality of the manufactured castings.
View More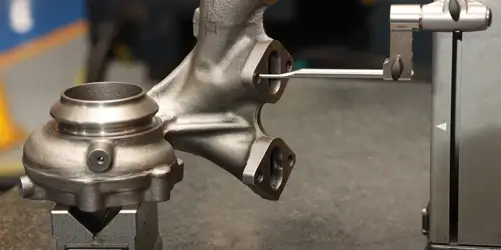
Testing and Quality Analysis
The precision and accuracy of the testing equipment is key to delivery of quality castings.
View More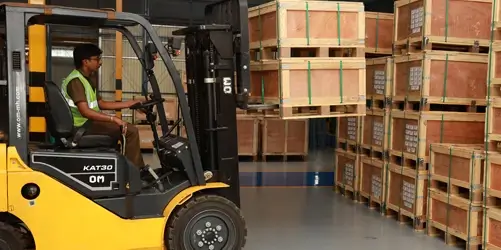
Packaging
JS Autocast uses Benchmarked standards for packaging to ensure safety and hygiene of the casting while shipment.
View More