Hydraulics
We manufacture all grades required for hydraulic and high pressure applications in SG grades with Cleanliness meeting the customer global standards and guaranteed resistance at low temperatures in complex parts. Our process capability enables us achieve Contamination requirements at <14mg/1000cm2. We manufacture high quality precision hydraulic motor covers, bearing support, bonnet, manifold, and elbow with weight ranges of 5 Kg upwards. We supply >160 variants across customers in Hydraulic applications.
Hydraulic Pump
Hydraulic Pump
The finest quality of Pump Castings impacts the estimated output across industries such as oil and gas, water treatment, agriculture, and other sectors. The company has gained a firm position in the industry as a Reliable Pump Investment Casting Manufacturer, holding clients across domestic and international markets. The firm practices world-class casting techniques to cast and supply critical pump parts.
There are a series of stages involved in the casting of pump components, which include pattern and mold design, Cast Iron composition selection, melting, pouring, solidification, finishing, quality testing, and end-product delivery. The efficient functioning and overall productivity of the Hydraulics Casting parts rely on the facility, technology, and other secondary contributors incorporated. The firm is integrated with the industry's latest discoveries to manufacture first-class Pump Casting products. JS Autocast has competitive advantages in engineering pump castings of various materials with defined specifications.
Hydraulics Ductile Iron Casting Process
The pump casting process includes the following basic steps:
Stages involved in the production of pump castings
- Heat-activated resin-coated sand is the fundamental core material preferred in the production of casting to forge the internal passage of pump casting.
- Depending on the technical and pattern requirements, the mold is forged with the assistance of an automatic molding machine.
- The internal structural detailing is ensured with sand casting methods, and high-precision molds are forged where the molten cast iron is poured into them for solidification.
- The manufactured casting parts are machined for a smooth and even surface finish to meet the customer's requirements of Hydraulics.
Valve Block
Valve Block
The Valve Block Iron Casting is one of the primary components that are assembled in hydraulic motors. It is a fundamental component and is assembled in the final drive motors and travel motors. The component has a simple design and delivers the normal functionality of directing and regulating the medium passed inward to reach the designated channel. The Iron Valve Block Casting is designed with the required port that serves as a case drain line, brake line, or two-speed line for efficient input and output flow.
Valve Block Application
The Cast Iron Valve Block provides a highly reliable and rigid connection between the valves and ports in the hydraulic motor. The component improves the overall performance and efficiency of the motor by controlling the generated pressure during the transfer of the medium. As the Valve Casting has a simple design, it enables easy installation and restricts the occurrence of leak points to a minimum. We, the Cast Iron Valve Block Manufacturer, follows stringent quality control to ensure every casting product is defect-free.
The transfer of fluids at the defined pressure and volume can be achieved with valve blocks. These components enable the working conditions to be adaptable when the fluid is sealed and regulated for discharge. Gate valves are quite unfeasible to regulate the flow as they are highly susceptible to eroding the parts assembled in the valve, such as the disk and seat, which is caused by vibration. Typically, Valve Block Castings are preferred to deliver the basic functioning of ON/OFF flow regulations.
Other Applications
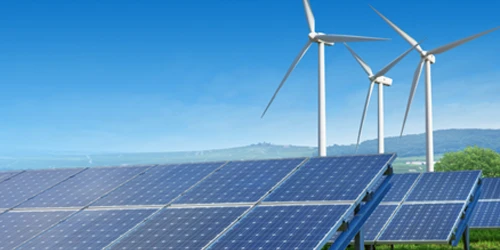
Wind Energy
The Worldwide wind market is becoming a vital source of power generation with a lesser carbon footprint.
View More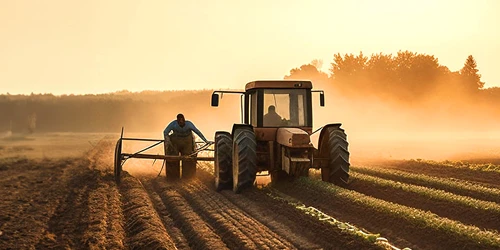
Agriculture
Manufacturing castings for the agricultural segment needs specialized expertise to meet the desired requirements.
View More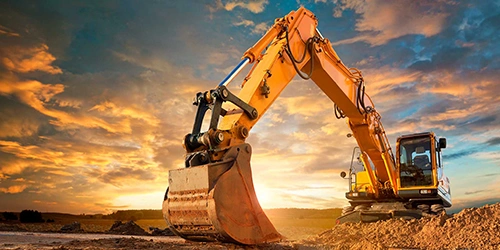
Off-Highway
The Off-Highway industry relies highly on large equipment and vehicles for operations and transportation.
View More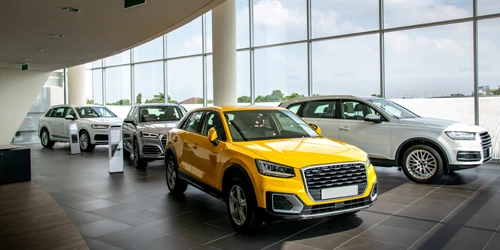
Automotive
The rapidly growing automotive industry in India is one of the largest in the world and it continues to grow at an incredible pace.
View More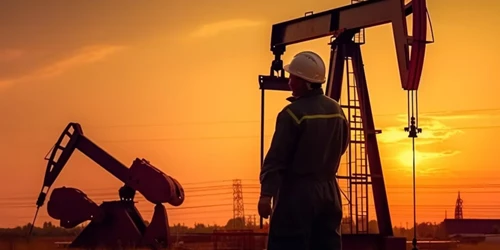
Oil & Gas
Each and every equipment in the oil and gas Industry are designed and manufactured with a chosen quality as it is the major contributor to the world economy.
View More