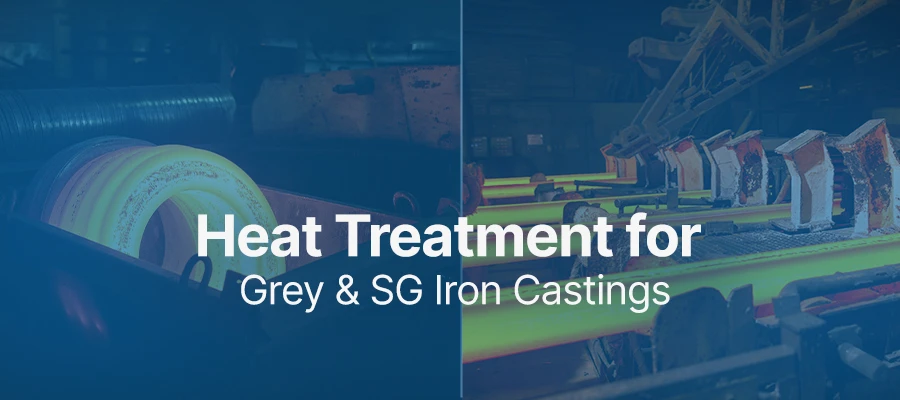
Heat Treatment for Grey & SG Iron Castings
December 30,2023
Metal heat treatment is an important process in mechanical manufacturing. It refers to metal thermal processing to get the desired structure and properties via heating or the soaking method.
The purpose of heat treatment is to change the microstructure of the material and improve its performance, including process performance, mechanical property, or a combination of both. The potential of the material can be fully utilized to improve the intrinsic quality of the part. Most cast iron parts and components are used by the automotive, construction, and electronics industries. The manufacture of these products is possible through different heat treatment techniques. Following are some of the heat treatment processes.
Stress Relieving
Stress-relieving is a heat treatment technique that subjects the cast iron to a constant temperature below its critical temperature before exposing it to controlled cooling. As the temperature gets higher, the mechanical properties of the cast iron typically change. Once the desired mechanical properties are achieved, the cast iron is then cooled. For most castings, a furnace cooling to 260°C can be done. Cooling to 95°C, alternatively, is a must for those that possess intricate shapes. This specific technique is applied to cast iron to effectively minimize residual stresses and dimensional changes.
Annealing
Another heat treatment technique that can be applied to cast iron is annealing. It is a heat treatment technique that changes the microstructure of the cast iron, therefore changing its mechanical characteristics. When applied to a cast iron alloy, annealing can easily reduce its hardness, increase its ductility, and eliminate internal stresses in the structure. Annealing is typically done by heating the cast iron for a specific time period before letting it cool slowly to room temperature. Various types of cast iron can go through different heating and cooling cycles to achieve distinct purposes.
Quenching and tempering
Both quenching and tempering are typically applied to cast irons to improve their hardness. But to yield great results, various parameters should be selected and controlled. Selecting and controlling the parameters, such as the temperature, can then prevent the cast irons from distorting, warping, burning, or quench cracking. Before performing these techniques, the heating of the cast irons must be done gradually to avoid inducing thermal stresses. The parts that were soaked must then be quenched. Tempering is subsequently done at a temperature range of 120 to 595°C.
When processing specific types of cast iron, different heat treatment techniques can be used. For example, high-alloy white iron castings can be processed through stress relief heat treatment and tempering. Grey cast irons and ductile cast irons, alternatively, can benefit from stress relief heat treatment and annealing at varying temperatures.
Normalising
Normalizing may be used to increase the mechanical properties, such as the tensile strength and hardness of grey iron-castings, or to restore (reclaim) the as-cast properties that got modified due to earlier heat treatment done deliberately or accidentally, such as graphitizing annealing, or the pre-heating and post-heating done for repair welding. Normalizing is the process of heating the grey iron castings to a temperature of around 885° to 925°C, soaking for a period of about 1 hour and 25 mm of the maximum thickness of the casting, and cooling in still air to room temperature. The microstructure of normalized iron consists of pearlite and graphite flakes.