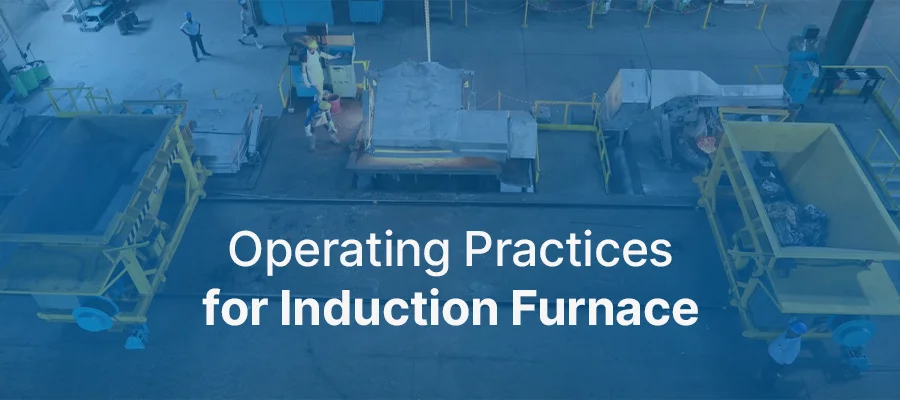
Operating Practices for Induction Furnace
September 4,2023
The electric induction furnace is a type of melting furnace that uses electric currents to melt metal. The principle of induction melting is that a high voltage electrical source from a primary coil induces a low voltage, high current in the metal or secondary coil. Induction heating is simply a method of transferring heat energy. Two laws that govern induction heating are: Electromagnetic induction and the joule effect.
The high frequency induction furnaces use the heat produced by eddy currents generated by a high frequency alternating field. The inductor is usually made of copper to limit the electric losses. The inductor is in almost all cases internally water-cooled. The furnace consists of a crucible made of a suitable refractory material surrounded by a water-cooled copper coil. In this furnace type, the charge is melted by heat generated from an electric arc. The coil carries the high frequency current of 500 to 2000 Hz. The alternating magnetic field produced by the high frequency current induces powerful eddy currents in the charge resulting in very fast heating.
A modern coreless induction furnace can melt a tonne of iron and raise the temperature of the liquid metal to 1450 °C using less than 600 kWh of electricity. Typically, specific energy consumption of coreless induction furnace varies from 500 to 800 kWh per tonne depending on type and grade of casting. The overall efficiency of induction furnace depends on many factors, such as: scrap charging system, furnace design, furnace cover, harmonics control, multiple-output power supply and refractory.
Best Operating Practices
Efficient operation of coreless induction furnace depends primarily on implementation of good/best operating practices. Best operating practices under each of stages are elaborated in following section.
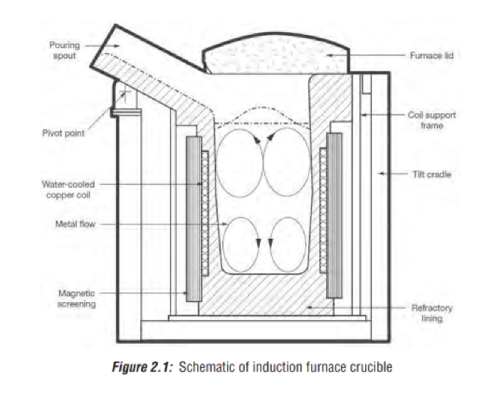
Charge
Preparation
Charging
Melting
Make the
melt ready
Emptying
the furnance
Charge Preparation and Charging
The raw material must be weighed and arranged on melt floor near to furnace before starting the melting.
- Charge must be free from sand, dirt, and oil/grease. Rusty scrap not only takes more time to melt but also contains less metal per charging. For every 1% slag formed at 1500 °C energy loss is 10 kWh per tonne.
- The foundry returns, runner and risers must be tum blasted or shot blasted to remove the sand adhering to it. Typically, runner and risers consist of 2 to 5 % sand by weight.
- Furnace should never be charged beyond the coil level, i.e., charging the furnace to its capacity. It should be noted that as furnace lining wears out the charging may slightly increase.
- Proper charge sequence must be followed. Bigger size metal first followed by smaller size and gaps must be filled by turnings and boring.
- Keeping exact weight of alloys ready, as alloys are very expensive proper handling will not only reduce wastage but also reduce time lost in alloying.
- The maximum size of single piece of metal/scrap should not be more than 1/3rd. of diameter of furnace crucible. It avoids problem of bridging. Moreover, each charge should be about 10% of crucible volume.
- There should no or less sharp edges, particularly in case of heavy and bulky scrap, as this may damage the refractory.
- Limit the use of baled steel scrap and loose borings (machining chips).
- Use charge driers and pre-heaters to remove moisture and pre-heat the charge. Vibro-feeders for furnace are equipped with vibrating medium and they could be fuel fired to pre-heat charge and remove oil/grease.
Energy Monitoring and Data Analysis
- Separate energy meter for furnace must be installed.
- Monitor energy consumption on heat-by-heat basis. Analyse them in correlation with production data to arrive at specific energy consumption of furnace on daily basis.
- Any peak or valley in data must be studied and investigated in conjuncture with tapping temperature and quantity of metal tapped.
- Energy monitoring is the first step for achieving energy saving.
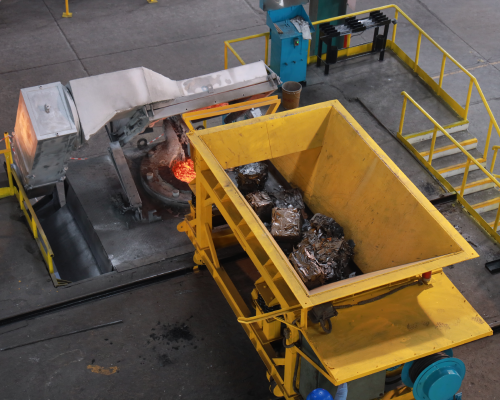