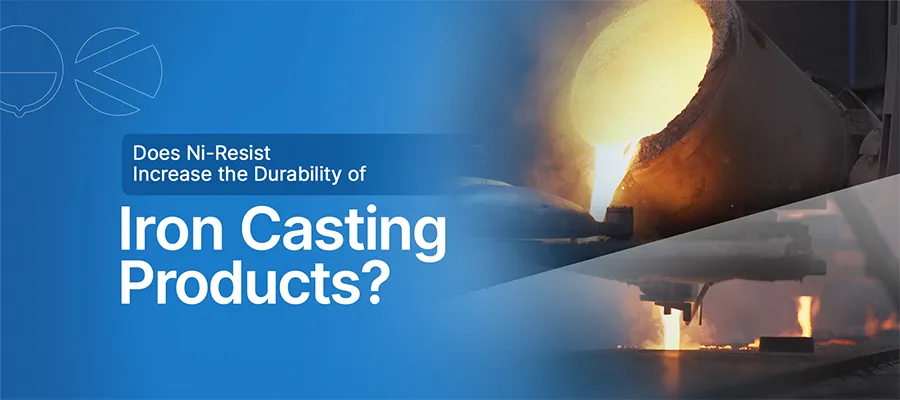
Does Ni-Resist Increase the Durability of Iron Casting Products?
Nickel is among the alloys with the highest quality and seamless functionality. The invention of castings with a combination of Ni alloys is happening at a faster pace. A small change in the proportion of the alloy generates a major difference in the technical properties of the end product.
The faster pace of casting industrialization has empowered the acquisition of market share when calculating the end product’s parts and components assembled. The cast iron has met the technical requirements infused with the design metrics.
The correlation between the design and functionality is mapped to analyze how the iron ore combination is efficiently set to improve the quality standards of the manufactured product.
Environmental Exposure
Corrosion development in the iron castings is inevitable. Iron products tend to degrade their resistance efficiency in the long run. It is typical when the product is subjected to a working condition where it is highly exposed to the environment.
With the right set of alloy combinations and proportions, the chance of corrosion can be reduced for many years. In order to obtain the required metrics, few alloys have the technical potential to improve corrosion resistance.
Thereby increasing the serviceability of the end product. Nickel ranks at the highest level for its outstanding property against corrosion.
Henceforth, the products deployed in working conditions with higher exposure to the environment are manufactured with nickel castings.
Durability
The product's durability is a measure of its value and effectiveness. It is the most considered technical property in the selection of raw materials and ores to manufacture iron casting products.
The endurance is the primary factor influencing the calculation of the serviceability of the castings. It is important to have the inbuilt capability and potential to resist corrosion without creating a change in the other properties.
In other words, castings are highly durable if they have the physical properties to serve their purpose until the estimated life period.
The infusion of nickel into the iron ore castings possesses a remarkable property in terms of durability. A small proportion of nickel alloy, varying from 5% to 10% in the casting ore mix, significantly transforms the durability of the castings.
Though the addition of Ni has a small share, it is the core material for achieving the desired quality requirements.
The Area of Application
Nickel castings have the greatest advantage of enhancing the quality of the end product. Ni does not propagate limitations and restrictions when it comes to the field of application. It has the nature of delivering its functionality irrespective of the seasonal conditions.
The integration of the iron castings may occupy a section of critical parts in the structural design of the end product.
The exposure to the outfield, with the varying working conditions and temperature, has an effect on the functionality of the casting part. Practically, the activities involved in the maintenance and replacement of parts or components assembled in the product lead to longer idle time.
There is a chance of impacting the entire supply chain operations and ending up decreasing profitability. There is a significant need for the reduction of replacements to eliminate the idle time involved in the chain of operations.
The parts and components with the alloy combination of nickel are primarily preferred in these working conditions. Ni has high resistance properties, which make it a suitable choice for manufacturing a product subjected to various applications.
Rough and Tough
Tensile strength has a direct relationship to the durability metrics of the casting. How? The part and component break down when withstanding the load of the product in the long run.
In addition, iron castings are renowned for their rugged properties, which in turn depend on the combination of alloys. Nickel has excellent tensile strength for withstanding rugged conditions.
Parts that are designed to withstand a higher working load are made of nickel castings. Technically, the greater the bearing capacity of tensile strength, the greater the tolerance of ductility.
Ni alloys restrict the chances of creating a deflection in ductility. Due to these advantages, agricultural machines and heavy equipment require the assembly of nickel castings.
Resistance
Resistance to corrosion and ductility without impacting the desired properties of iron castings is technically possible to achieve with nickel alloy combinations.
These technical advantages add value to the core investment and lead to the creation of unique spaces for designing and developing innovative products.
The preference for Ni is upscaling, and it will be the primary alloy element in the manufacturing of castings.
The Bottom Line
We guess this article has justified the title by covering the most important topics essential to determining the impact of Ni alloy on the enhancement of casting durability. JS Autocast is one of the foundries with the state-of-the-art infrastructure to manufacture Ni-Resist Castings. please go to for more information.