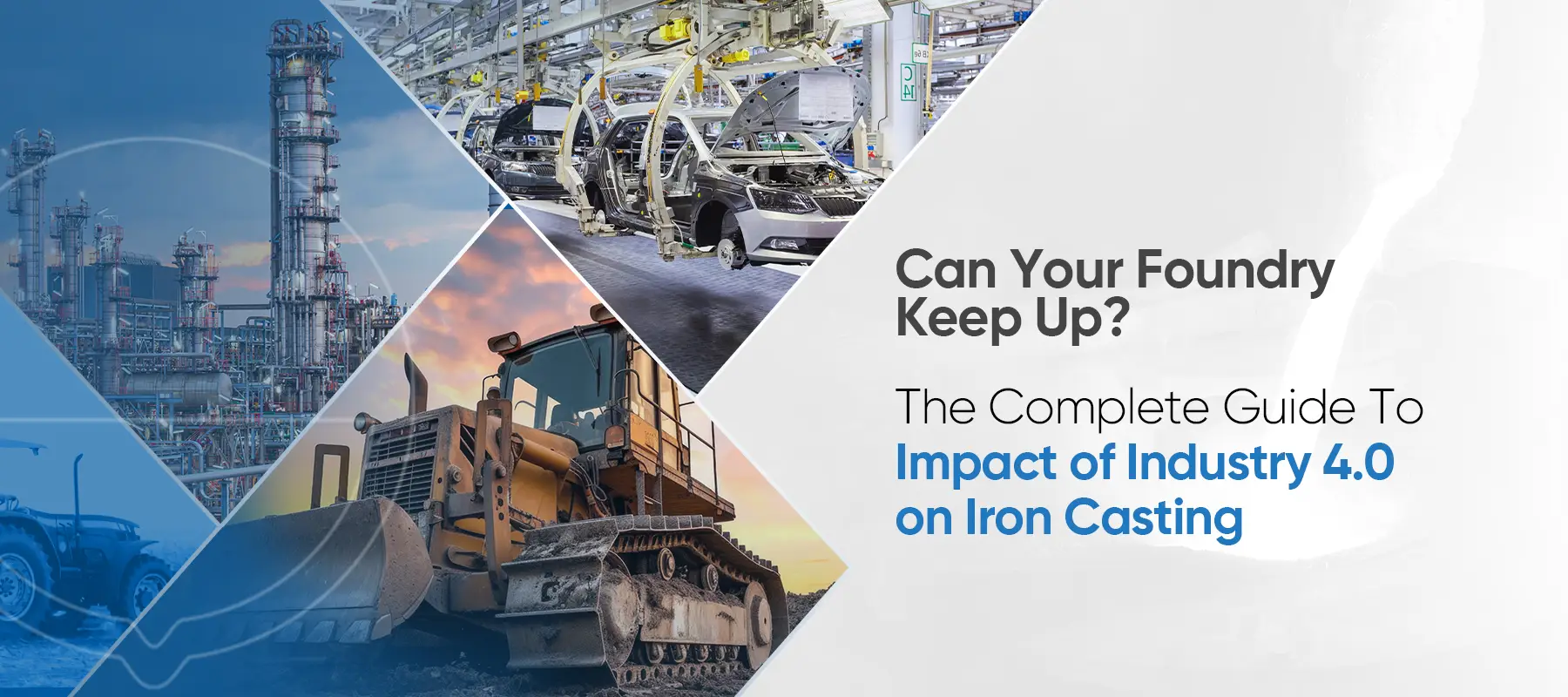
Can Your Foundry Keep Up? The Complete Guide To Impact of Industry 4.0 on Iron Casting
Imagine where your foundry can predict failure even before it happens, reduce manufacturing costs and boost overall productivity. Sounds like a dream, doesn’t it?
But all this is possible with the power of smart technology. Yes, with the manufacturing world constantly evolving, the future of iron casting is not much far away.
With a perfect mix of technology, automation and data-driven decisions; Industry 4.0 has opened a new door to a smart future. With Smart foundry technology, IoT in metal casting and others, this revolution has changed the path of the manufacturing industry from just new innovations to unlocking the true potential.
What does your foundry do to keep up with the latest trends? In this blog, let’s find out the latest innovations in the industry and how to be future-ready.
Industry 4.0 — What Is It And How It’s Shaping Iron Casting?
You might think: It is just a trend. But it is not. It is a change in the mindset. In the 4th Industrial Revolution (Industry 4.0) digital, physical, and biological systems blend together.
This would mean iron casting gets — an integration of intelligent, connected systems that enhance all aspects of production. From the casting mould to predictive maintenance, these systems will be designed to improve the efficiency of foundries.
This revolution has brought in smart foundry technology that manages and controls the data in real-time.
Think this through: Can you afford to ignore automation in iron casting when you know that it brings you numerous benefits?
Key Benefits of Industry 4.0 In Iron Casting
The benefits of blending Industry 4.0 in iron casting practices are innumerable. Let’s break it down:
- Improved Efficiency And Productivity : You get to save on manual labour. With machines in line at work, people get to focus more on strategic matters, while the machines work in less time than a human would, saving on lead time.
- Predict Maintenance Time : With the IoT in metal casting, real-time data from a machine helps catch early wear and tear or a potential breakdown. This proactive approach to maintenance helps to understand the time and cost taken for maintenance.
- Cost Benefits : Using automation and predictive technologies will actually help a business minimize resource waste and ensure optimum use of materials, directly impacting the bottom line.
- Quality Of Product Improved : With automation, consistency is achieved in the casting process. This ensures that the products are of high quality with a reduced defect rate. This is crucial in high-precision industries like automotive and aerospace.
Are you ready to make the most of these benefits and improve your competitive edge?
Technological Advancements Shaping The Iron Casting Industry
Just talking about automation or IoT is never enough – it is more about understanding these technologies and how they transform the iron-casting foundries. Here are some technologies –
- Smart Foundries : With the rise in smart foundry technologies, factory units are becoming smarter and more automated. With this iron casting automation trends, you can control the processes and adjust the process remotely to get maximum productivity.
- Predictive Maintenance Through IoT : With sensors in the machine, data can be taken in real-time which helps to reduce failures and optimise schedules. This way you can increase the life span and reduce downtime.
- AI Automation : With AI, you can predict the demand and adjust the manufacturing process in real-time based on customer needs.
- 3D Printing : 3D printing is transforming the way iron foundries are producing complex parts. It allows to create intricate designs with minimal wastage which in turn reduces material costs and lead time.
Can your foundry afford to work without these advanced technologies and get left behind?
What Are The Challenges?
Every strength has its own weakness, and so does Industry 4.0. The challenges include —
- The Cost : Adopting to new and advanced technology requires an enormous amount of money. But, no matter what, the short-term challenge is nothing in front of the long-term benefits.
- Gap In Skills : With new technologies in the ground, your workforce needs to update themselves with the latest technology. Without proper training, it can be quite difficult to manage.
- Security Concerns : With so much advancement, foundries now might face cyber security issues. It is important to secure the data and infrastructure with solid security systems.
What’s The Future?
The future growth within the iron casting industry is huge with Industry 4.0. In further future, we can see –
- More Automation : We can expect more automation in the future which will 2x the efficiency.
- Machines Become Smarter : With new technologies, machines can learn and evolve from data and processes with minimal human disruptions.
Think about this: How much more efficient can your system become with these technological advancements?
Closing Remarks
Blending your company with Industry 4.0 in iron casting is no longer an option — it is a must. Foundries that adopt to these technologies will find themselves ahead in the competition where productivity and efficiency are at the top.
With quick changes in the industry, it is no longer about adopting or not adopting to the technologies but more about how quickly you act on it.
Don’t wait anymore! The industry revolution has already started — when are you taking your step?
For more industry trends and tips, reach out to us today!