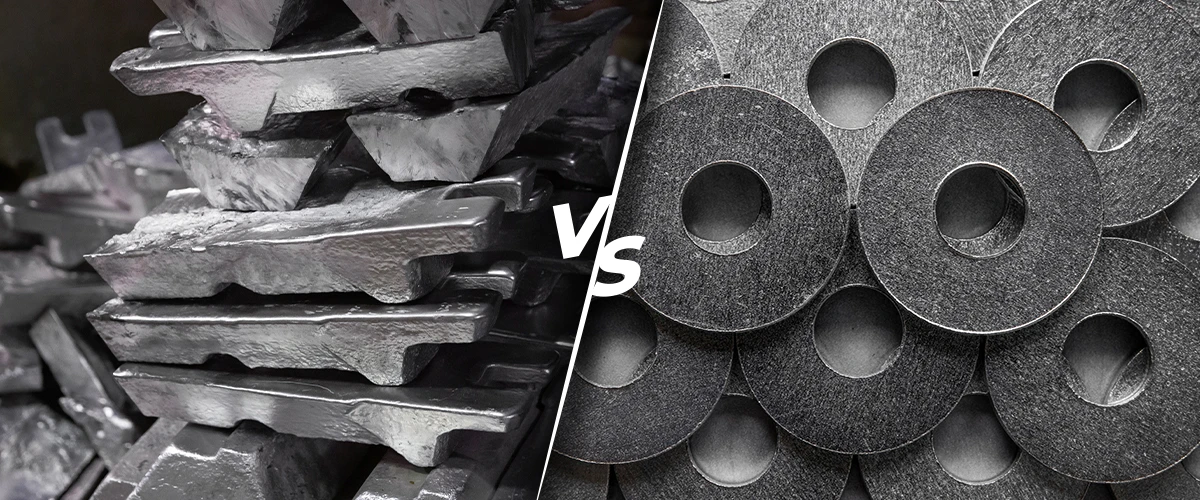
Grey Iron Casting vs. Ductile Iron Casting
June 25,2023
In the manufacturing industry, the casting business is making huge steps forward. Casting is becoming the most popular way to make engineering parts and components, both simple and complicated.
In the world we live in now, new findings would not be possible without casting technology and solutions. Iron casting has made it easier to make important parts for many different businesses.
Each part of a machine has a job to do for the machine as a whole and for it to work well. Iron has been the most important ore for making things that are strong and last a long time.
No one has yet found a good replacement for iron. When ores are mixed with iron, new metals are made.
Iron Ores
Grey iron and ductile iron are the two types of iron rock that are most often used to make cast parts. Changes in how people feel about things happen over time.
Before ductile iron was found, it’s likely that grey iron ruled the casting business for a long time. Every kind of material has a different product life cycle.
The market demand for iron ore is affected by the pros and cons of the end product made from casting material. In many scientific ways, ductile iron has been better than grey iron.
Tensile Strength
One of the most important technical qualities of steel and iron products is their tensile strength. Tensile strength is a very important factor in figuring out how long a part or component will last.
The more useful something is, the higher its tensile strength. The tensile strength of ductile iron is 60000 psi, which is much higher than the 20000 psi tensile strength of grey iron. When making parts and components, the result goes through different stages of machining and using tools.
Because the parts of ductile iron castings have a high tensile strength, they can be cast and machined precisely within the tolerance level.
Vibration Resistance
All of the bits and pieces that make up the machine vibrate. How much the part vibrates depends on how well it fits together.
Technically, ductile iron castings can handle vibrations better than grey iron castings. The final product fails because it can’t handle the vibrations that happen while it is working.
When castings are made with dutile iron, the amount of damage caused by vibration is reduced to its lowest level.
Higher Strength
The way things are put together depends on how the product is made. The strength of the mould is just as important as any other technical property. Changes in load caused by the end product’s ongoing operation affect how well and how long the casting will last.
The grey iron castings are not as strong as the ductile iron castings. The performance of the finished product is also affected by how strong the castings are.
Most of the time, ductile iron castings are the best choice for making parts and components that need to be very strong.
Industrial Applications
Castings are used in many industries in important ways. Castings found their niche by making important parts for many different businesses.
The businesses that use ductile iron casting the most are automobiles, agriculture, mobile heavy equipment (MHE), and oil and gas.
Unlike grey iron castings, ductile iron castings can be machined with precision and accuracy, which has been one of the best things about using them in industry.
Resistance to heat
When working with other parts and pieces, industrial tools usually produce heat. The heat that is made could change the tolerance level of the cast parts, which could affect how well the whole thing works.
So, the iron rock material that is used to make castings has to stop heat from moving from one part to another. In the business world, castings with thermal protection are in high demand.
The heat resistance of a cast product makes sure that the tolerance level stays the same while the product is in use. Castings made of ductile iron have been shown to be more resistant to heat than those made of grey iron.
Ductile iron is used to make casts that need to be able to work at higher temperatures.
In Conclusion
When it comes to its technical qualities, ductile iron is better than grey iron. When it comes to making an investment, grey iron is cheaper than malleable iron. But if the most important thing is to make high-quality cast products, then using malleable iron to make cast products is the best way to make more money since cast products are highly valued. If you work for a manufacturing company and are looking for a ductile iron casting maker, JS Autocast is one of the most trusted ductile iron casting manufacturers in the business.