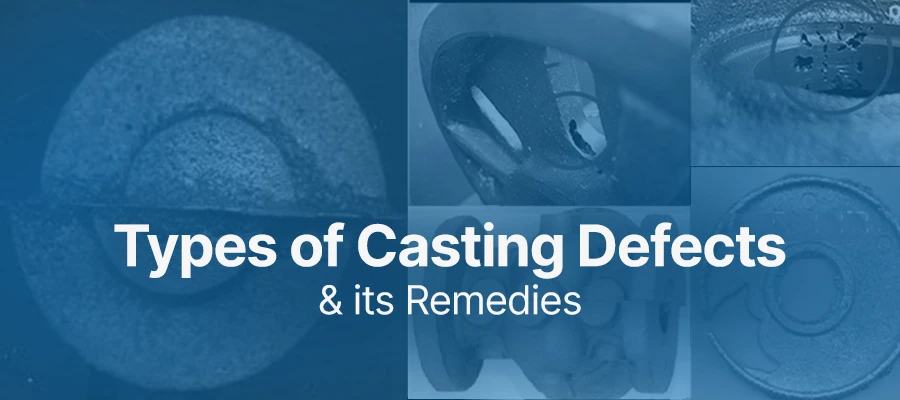
Types of Casting Defects & its Remedies
Casting is a process that carries a risk of failure throughout the entire process of completing the finished product. Hence, necessary action should be taken during the manufacturing of cast products so that defect-free parts are obtained. Most casting defects are concerned with process parameters. Hence, one has to control the process parameter to achieve zero defect parts. Casting defect analysis is the process of finding the root causes of the occurrence of defects in the rejection of casting and taking the necessary steps to reduce the defects and improve the casting yield. In this review paper, an attempt has been made to provide all casting-related defects with their causes and remedies.
During the process of casting, there is always a chance that a defect will occur. Minor defects can be easily salvaged, but high rejection could lead to significant change at a high manufacturing cost. Therefore, it is essential to identify the exact root cause and its remedies.
The common defects in grey and ductile iron castings are:
Blowhole
A blowhole is a cavity defect that is also divided into a pinhole and a subsurface blowhole. A pinhole is a very tiny hole. Subsurface blowholes can only be seen after machining. Gases are entrapped during the solidification of a metal in the casting, which results in a rounded or oval blowhole as a cavity. Frequently associated with slag or oxides. The defects are nearly always located in the cope part of the mould, in poorly vented pockets and undercuts.
Sand inclusion
sand inclusion and slag inclusion are also called scab or blacking scab. They are inclusion defects. Irregularly formed sand inclusions, close to the casting surface, combined with metallic protuberances at other points. Sand inclusion is one of the most frequent causes of casting rejection. It is often difficult to diagnose, as these defects generally occur in widely varying positions and are therefore very difficult to attribute to a local cause. Areas of sand are torn by the metal stream and float to the surface of the casting because they cannot be wet by the molten metal. Sand inclusions frequently appear in association with CO blowholes and slag particles. Sand inclusions can also be trapped under the casting surface in combination with metal oxides and slag and only become visible after machining. If a loose section of sand is washed away from one part of the mould, metallic protuberances will occur here and must be removed.
Misrun
A misrun defect is a kind of incomplete casting defect that causes the casting to be uncompleted. The edge of the defect is round and smooth. When the metal is unable to fill the mould cavity completely, it leaves an unfilled portion called a misrun. A cold shunt is called when two metal streams do not fuse together properly.
Remedies
- Adjust the proper pouring temperature.
- Modify design.
- Modify the gating system.
Gas porosity
The gas can be from trapped air, hydrogen dissolved in alloys, moisture from water-based die lubricants, or steam from cracked cooling lines. Air is present in the cavity before the shot. It can easily be trapped as the metal starts to fill the cavity. The air is then compressed as more and more metal streams into the cavity, and the pressure rises. When the cavity is full, it becomes dispersed as small spheres of high-pressure air. The swirling flow can cause them to become elongated.
Remedies
- Increase the metal-pouring temperature.
- Modify the metal composition to improve fluidity.
- Pour metal as rapidly as possible without interruption. Improve mould filling through modification.
- to running and gating systems.
- Remove slag from the metal surface.
Shrinkage
Shrinkage defects occur when feed metal is not available to compensate for shrinkage as the metal solidifies. Shrinkage defects can be split into two different types: open shrinkage defects and closed shrinkage defects. Open shrinkage defects are open to the atmosphere; therefore, as the shrinkage cavity forms, air compensates. There are two types of open-air defects: pipes and caved surfaces. Pipes form at the surface of the casting and burrow into the casting, while caved surfaces are shallow cavities that form across the surface of the casting. Closed shrinkage defects, also known as shrinkage porosity, are defects that form within the casting. Isolated pools of liquid form inside solidified metal, which are called hot spots. The shrinkage defect usually forms at the top of the hot spots. They require a nucleation point, so impurities and dissolved gas can induce closed shrinkage defects. The defects are broken up into macroporosity and microporosity (microshrinkage), where macroporosity can be seen by the naked eye and microporosity cannot.
Remedies
The general technique for eliminating shrinkage porosity is to ensure that liquid metal under pressure continues to flow into the voids as they form.