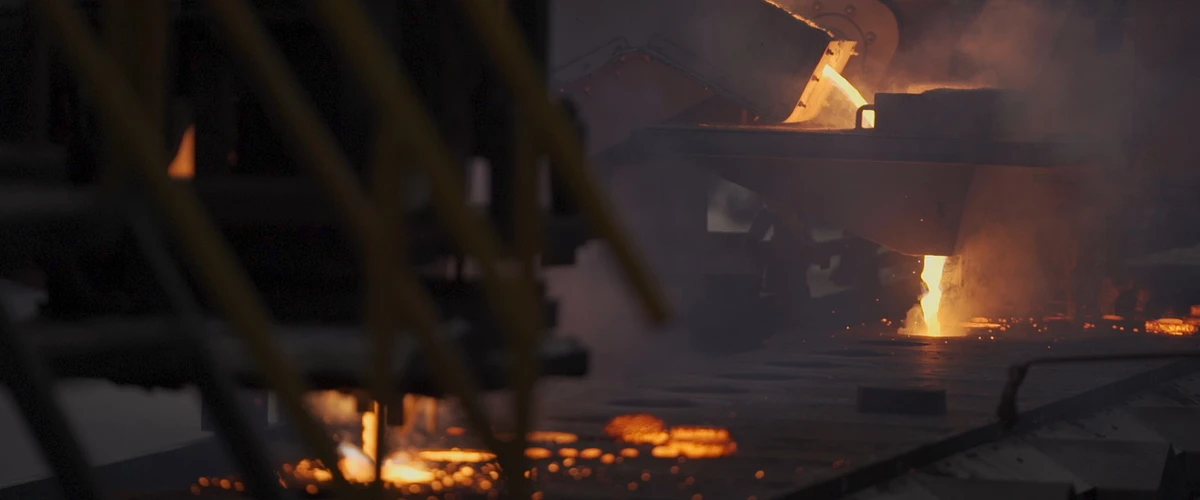
Austempered Ductile Iron(ADI)
August 12,2023
ADI is a special type of cast iron. It exhibits higher wear resistance, tensile strength, and toughness than other ductile irons. An alloyed ductile iron along with elements like Molybdenum, Nickel and Copper is heat treated using the austempering method to give it special characteristics.
The metal matrix is the primary determinant of the mechanical characteristics in ductile iron and ADI. In traditional ductile iron, a regulated blend of ferrite and pearlite makes up the matrix.
A superior set of advantages such as low cost, design flexibility, good machinability, high strength-to-weight ratio, and good toughness, wear resistance, and fatigue strength is provided by ADI grade castings.
It offers all the production benefits of a typical Ductile Iron casting since it may be cast like any other member of the family. It is then put through the austempering process to give it mechanical qualities that are better than those of traditional ductile iron, many cast and forged steels, and cast and forged aluminum.
The distinctive acicular ferrite and Ausferrite (carbon stabilized austenite) matrix that makes up ADI essentially gives it these special qualities.
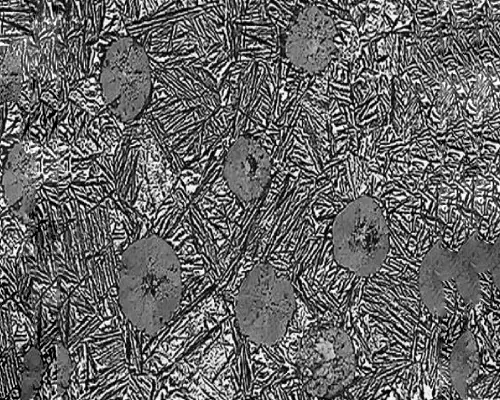
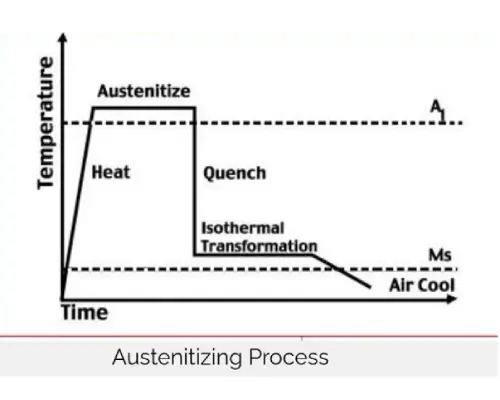
The Austenitizing Process in Steps
- Castings should be heated to an austenitizing temperature in a molten salt bath.
- To dissolve carbon in austenite, the temperature is kept at the austenitizing range.
- The metal matrix is Immediately quenched to prevent pearlite formation.
- Castings are held in molten salt bath at austempering temperature for isothermal transition to ausferrite.
Through a complex heat treatment procedure, the metallurgical structure of austempered ductile iron is improved. Parts with high strength, abrasion resistance, greater ductility, and toughness are produced using austempered ductile iron.
Austempered Ductile Iron has the following benefits:
High strength, Exceptional toughness, Superior wear attributes, good fatigue properties, and cost effectiveness.
- Strength in Tensile and Yield
The tensile and yield strengths of ADI are at least twice as high as those of conventional ductile irons - Fatigue Strength
When compared to ordinary ductile irons, ADI typically has a fatigue strength that is 50% higher. By using fillet rolling or shot peening, it can be strengthened even further. The ADI grades with lower hardness are suitable for structural applications - Toughness
ADI is perfect for applications like ground-engaging tools due to its strong impact and fracture-toughness qualities. - The higher ADI hardness classes are ideal for wear applications due to their outstanding wear characteristics. The ADI is normally equally hardened throughout the part, unlike case-hardened materials. Also, under pressure, ADI works even harder. This creates a surface of martensite that is extremely hard where wear resistance is most required.
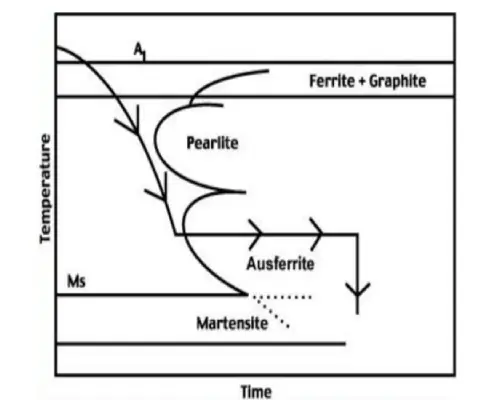
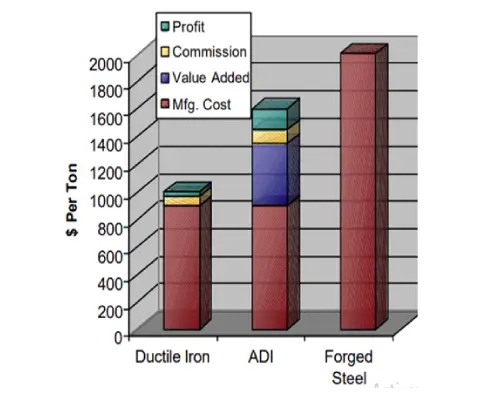
Cost-effectiveness:
- • In comparison to steel forgings or castings, ADI is typically 15% to 20% less expensive. The most cost-effective method for achieving tensile, yield, or fatigue strength is this.
- • For heavy-duty applications where dependability is essential, ADI frequently compares favorably with heat-treated and alloy steels. It is a beneficial improvement above ductile iron’s regular grades.
- • It can sometimes take the place of nickel-chrome iron and manganese steel. Where the design allows for a smaller section, ADI has even substituted aluminum due to its superior strength-to-weight ratio